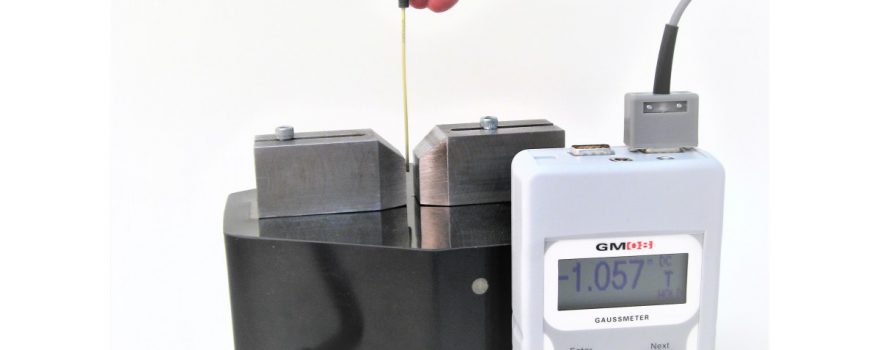
Why magnetic validations are necessary – trends that can cause problems
-
When analyzing existing and potential foreign material hazards, metal fragments are consistently identified as a major concern. When discussing food safety with quality assurance personnel, foreign material-related incidents are the most frequent hazards identified in the food industry today
-
The bulk of metal and magnetic fragments of concern in today’s food processing are <3mm and down to 100 microns in size, such particles and fragments originate from several sources such as, supplier raw materials, wear and tear of processing machinery and from maintenance activities
-
It is good practice to extract these contaminations with powerful magnets prior to metal detection and X-ray equipment, because:
-
Metal detectors trip
-
Metal detectors often miss particles smaller than their “test piece” size and small wires (if not fortunately oriented transverse in their passage through the detector’s search coil)
-
Without use of efficient and effective upstream magnet installations, product food safety and brand integrity are in jeopardy
-
-
It is necessary to develop, implement, and maintain an effective magnet verification program because magnets CAN and DO lose strength over time – even very rapidly under some conditions of use
Potential risks and consequences of inferior magnets which do not meet today’s standards include
-
Product Contamination
-
Consumer Injury
-
Product Recall
-
Brand Name Risk
-
Equipment Damage/Failure – High Impact
-
Product Contamination
-
Loss of Product
-
Down Time
-
Costly Repairs, and
-
Ongoing Maintenance
Additional risks related to inferior or ineffective Metal Fragment Control programs include
-
Malfunctioning
-
De-Sensitization
-
Product Wastage
-
Nuisance Trips, and
-
Down Time
The benefits of using a Gauss Meter for magnet verifications
-
The Gauss Meter is used increasingly in the food industry because of is accuracy and ability to verify, validate, and accurately compare strength loss trends over time
-
Gauss Meter technology is being rapidly adopted by major food companies because it does give a more definitive and specific measurement
-
The Gauss Meter is suitable for testing a wide range of magnet strengths between 1,000 and 13,000 Gauss. This test method is endorsed by HACCP International
The Gauss Meter test
-
Used increasingly in Food Industry since 2010
-
Definitive, Accurate, Repeatable, Calibrated
-
Plate Magnets now used less in food industry
-
Surface strength of magnets is generally 10,000 Gauss now for product security in food industry
-
No safety issues with Gauss Meters
-
Gauss Meter Test conforms to current standards for final Magnets in food industry
The benefits of our magnet verifications above that of our competitors
-
We are an independent external body and perform magnetic verifications at a minimum of every 12 months
-
Our magnet verifications are conducted with a calibrated Gauss Meter using properly endorsed procedures, rather than dated and often inaccurate pull test calibrated methods
-
We supply a record that includes the testing results and traceability certificate of the Gauss Meter used
-
Validation activities are performed per defined requirements. This activity provides the data (objective, evidence, records) that the magnets are effectively controlling the hazards
-
We identify and maintain records to confirm compliance that magnets continue to meet current magnet specifications for performance and effectiveness
-
We deliver a quality HACCP endorsed report containing realistic, and practical magnetic separation solutions keeping you aware of the latest technology to assist you in maintaining product security and brand protection
Our Magnetic Validations include a magnet verification/validation report with the annual calibration provided by an independent third-party specialized magnet service provider that
-
Confirms individual magnets meet current standards
-
Confirms whether individual magnets are still as effective as when first installed,
-
Provides the estimated coverage and magnetic strength for each magnet,
-
Identifies potential risk of metal contamination
-
Provides specifications to address magnet needs
2018-08-24
Categories:
Leave a Reply